REVOLUTIONARY PROCESS
NEW PERFORMANCE ORGANIC COATING
Aramfix exclusively supplies corrosion protection Ecomet Corundum, made in the EU.
Our zinc flake corundum technology is the next generation developed to provide superior corrosion protection for metal surfaces, enhance their durability, improve their performance, prevent rust, increase chemical resistance, and reduce friction during installation. Our organic coating replaces the polluted electroplating mechanism, thereby stopping the discharge of the pollutants, crafting both water-based and solvent-based coatings.
Zinc flake corundum technology is ideal for use in a wide range of applications, including automotive, aerospace, marine, and industrial applications.
All our items are rigorously tested and meet the highest international standards, ensuring unmatched reliability and consistency!
info@aramfix.com
π Limited Time Offer β Donβt Miss Out! π¨
PRECISE THIN COATING LAYERS
PRECISION AND EFFICIENCY
RANGE OF DIP SPIN MACHINES
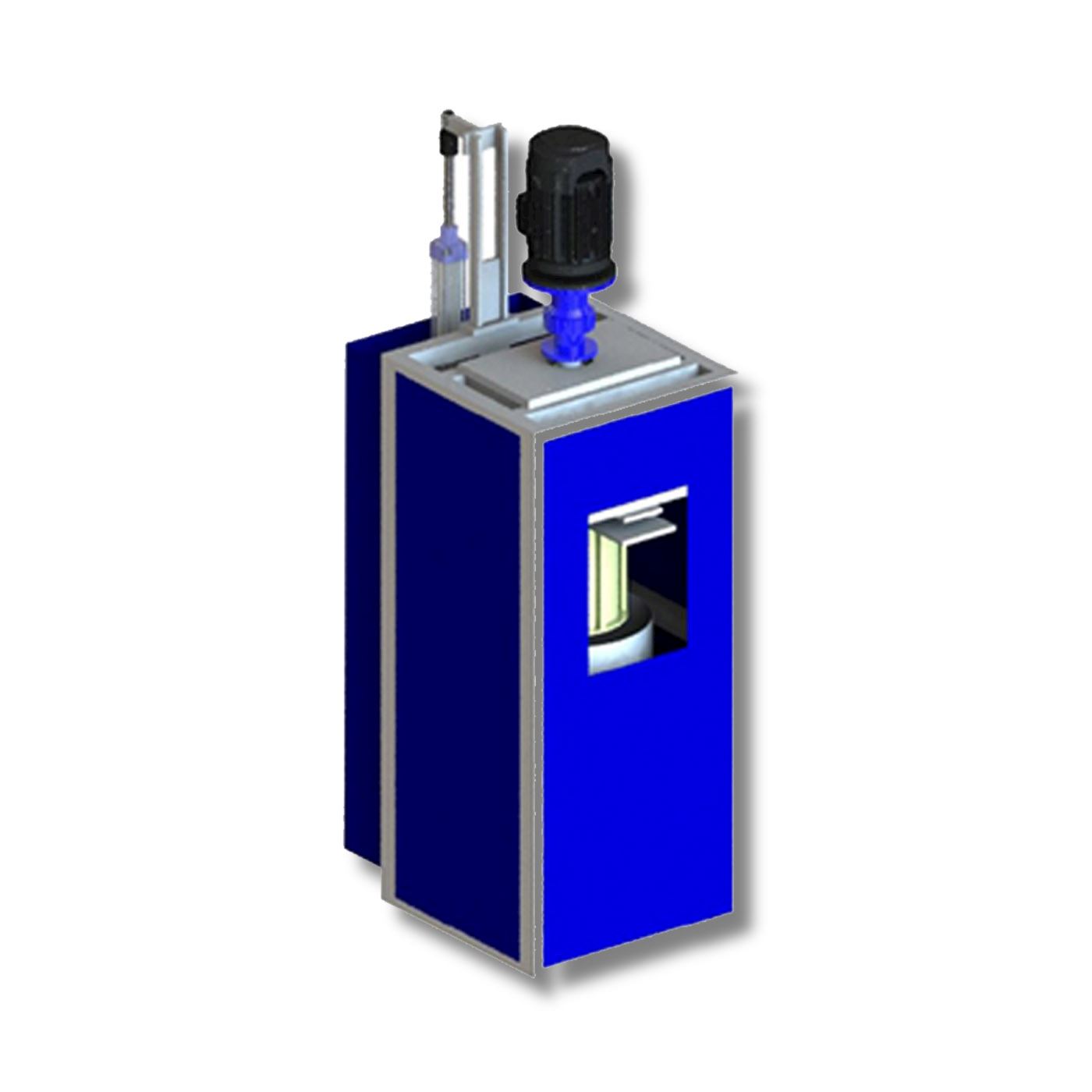
DS 200
EFFCO DS-200 Dip-Spin Coating Machine
200mm basket
LxWxH 1000x1000x1800mm
New generation simplified Automatic dip spin coating application equipment technology.
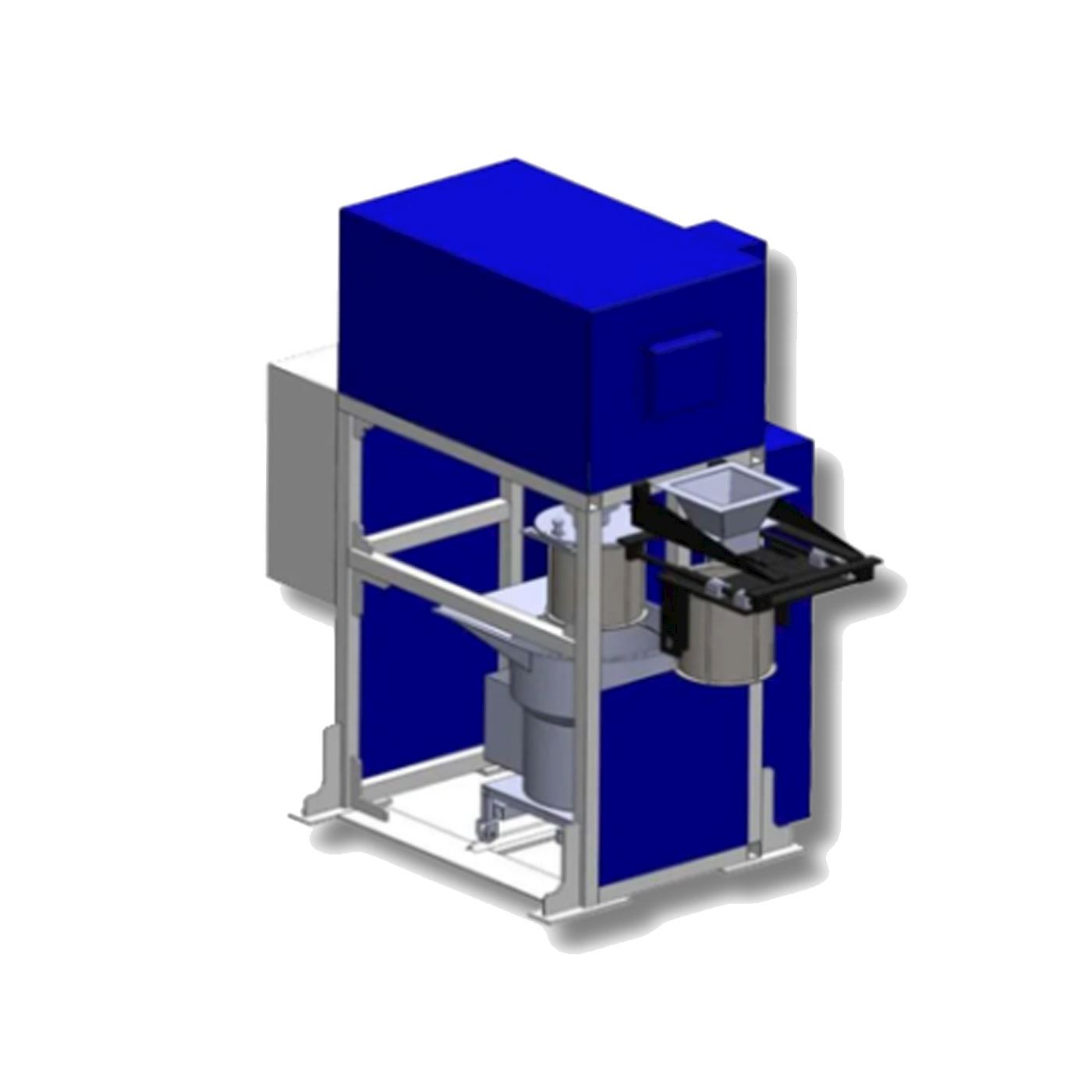
DS 250
EFFCO DS-250 Dip-Spin Coating Machine
250mm basket
LxWxH 1500x1500x1890mm
New generation simplified Automatic dip spin coating application equipment technology.
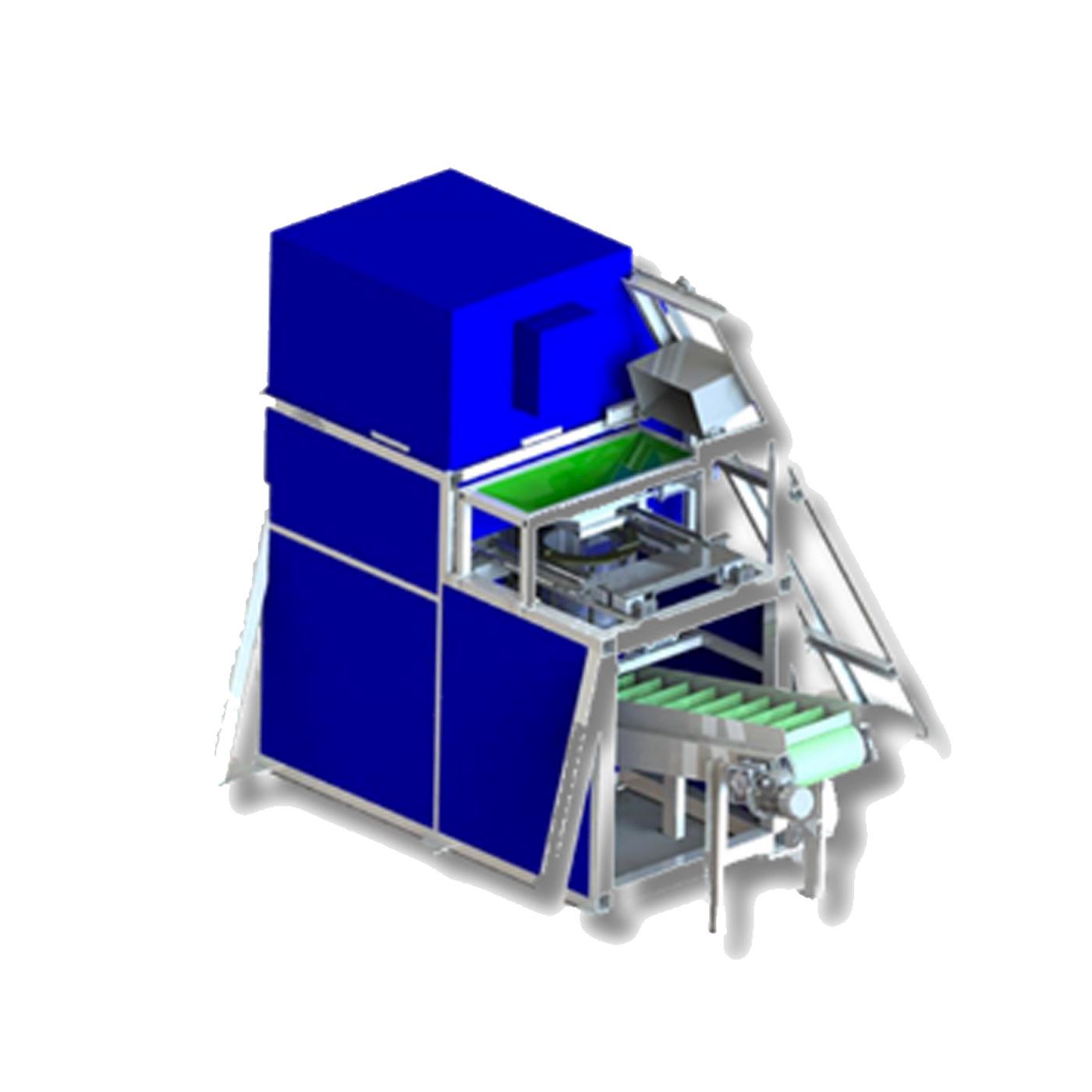
DST 400
EFFCO DST-400 Dip-Spin Coating Machine
400mm basket
LxWxH 2800x3500x2300mm
New generation simplified Automatic dip spin coating application equipment technology.
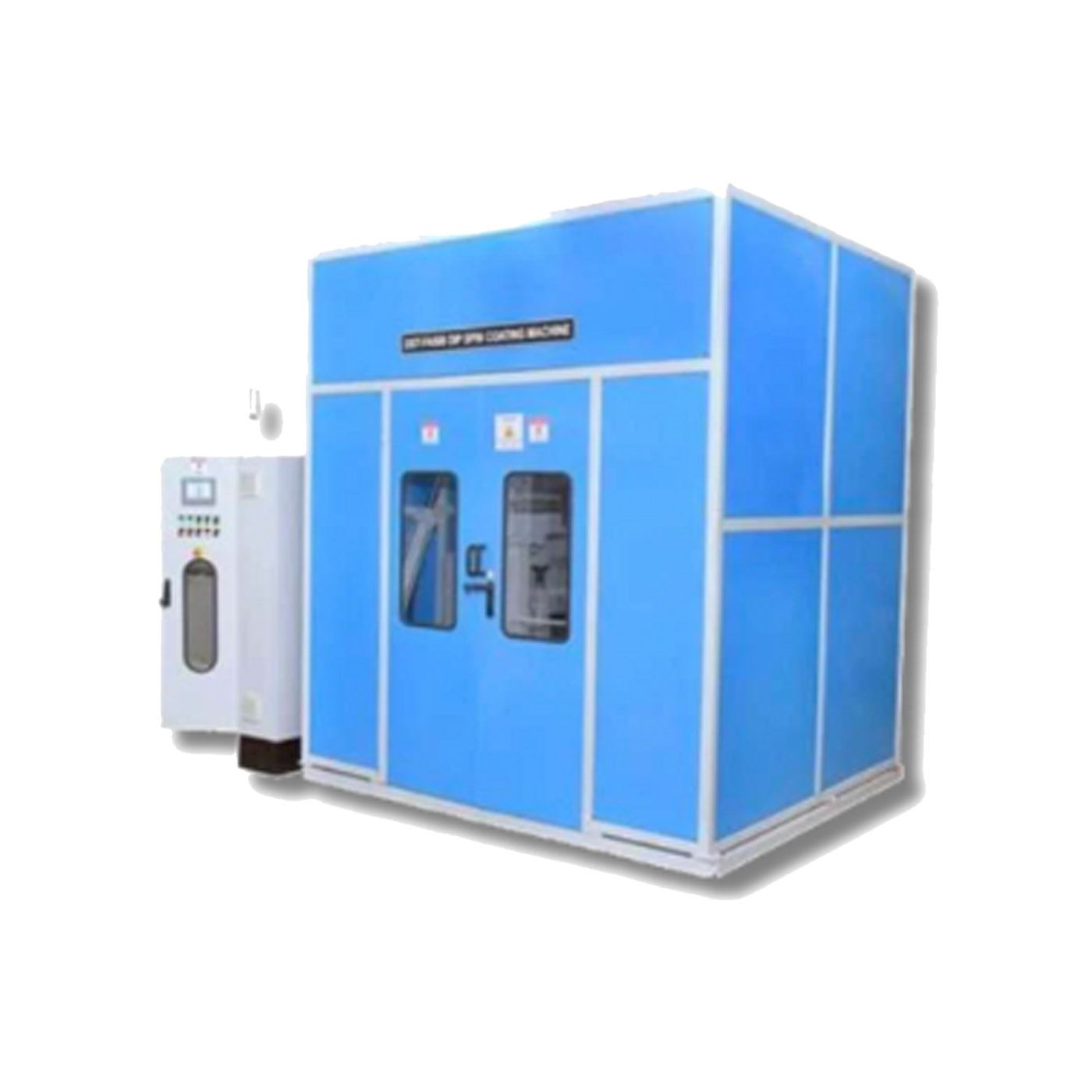
DST 500
EFFCO DST 500 Dip-Spin Coating Machine
500mm basket
LxWxH 2900x2900x3200mm
New generation simplified Automatic dip spin coating application equipment technology.
INNOVATIVE SURFACE COATINGS
INNOVATION AWARD WINNING CORUNDUM
WITNESS THE FUTURE
DIN EN ISO-10683/ASTM-F3393
Over 2000-6000h SST-30 yrs of corrosion protection
EXTEND COMPONENTS LIFE
ZINC-FLAKE COATING
Looking for longevity and durability of your components? Act today before risk ruins the whole structure!
ECOMET Corundum, a state-of-the-art zinc flake coating with a corrosion rate as low as 0.02-0.03 microns per year and withstanding up to 6,500 hours of salt spray testing, itβs built to protect your components against extreme temperatures, chemicals, and humidity, ensuring long-lasting durability.
Zinc flake coating is applied through a non-electrolytic process, typically using techniques like dip-spin, rack dip-spin, or spray application.
This process ensures precise, consistent application without the risk of hydrogen embrittlement, offering superior protection compared to traditional methods. It offers a thinner, more precise layer, ensuring better corrosion resistance and avoiding these drawbacks.
The whole process is environmentally friendly, free from acids and pollutants.
We have already adviced offshore projects, automotive applications, onshore construction, chemical plants to increase lifetime. Contact our specialist M. Wirken for your project!
FREE FROM CHEMICALS
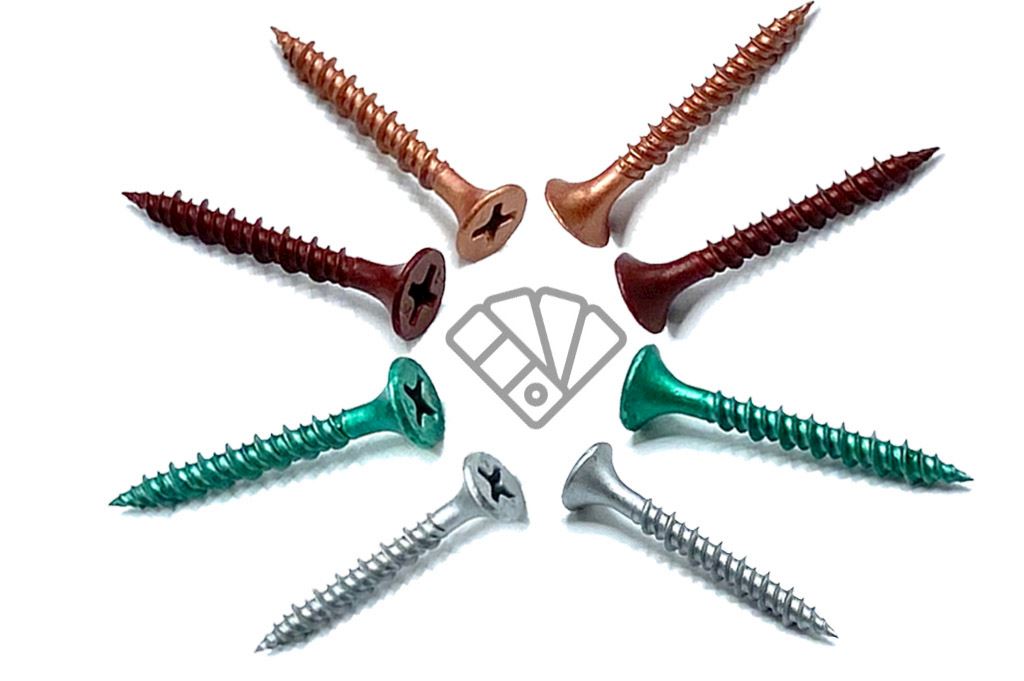
ECOMET WATER REDUCTIBLE TOPCOAT SERIES
EFFCO Fastener Coating Products as per ISO-10683/ASTMF-1136
Water-reducible hydrophobic topcoat sealer for base coats like ECOMET 500, Zinc plating, and other zinc-based surfaces. The coating is applied by dip-sin or spray and then cured in an oven at 200 degrees C for 25 minutes.
ECOMET WATER REDUCTIBLE COATING SERIES
EFFCO Fastener Coating Products as per ISO-10683/ASTMF-1136

ECOMET 500
Water reducible nano zinc aluminium flake chrome VI free coating for anti-corrosive application by dip spin or spray. The coating comes with A, B and C as a 3-pack system. It needs to mix before application by dip spin or spray. Curing temperature is 330 deg c for 30 mins
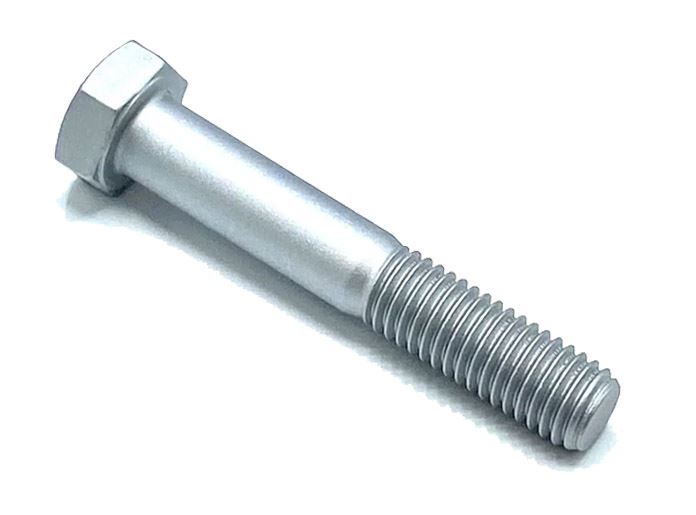
ECOMET TOP SILVER
Water reducible hydrophobic topcoat sealer for base coats like ECOMET 500, Zinc plating and other zinc-based surfaces. The coating is applied by dip sin or spray followed by curing into oven for 200 deg c 25 mins.
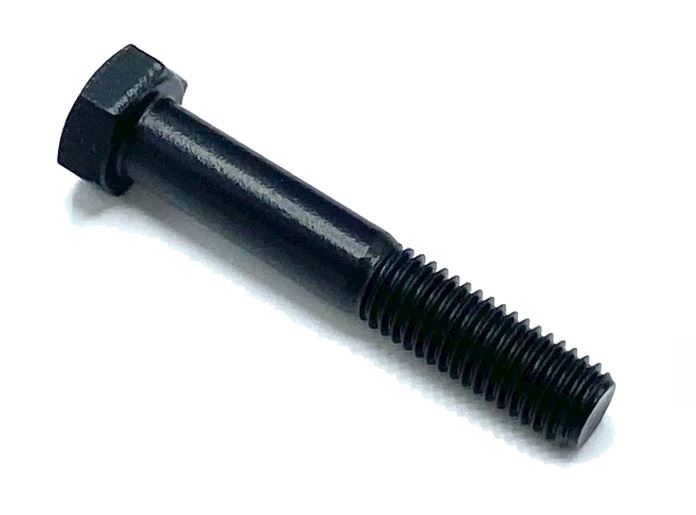
ECOMET TOP BLACK
Water reducible hydrophobic topcoat sealer for base coats like ECOMET 500, Zinc plating and other zinc-based surfaces. The coating is applied by dip sin or spray followed by curing into oven for 220 deg c 25 mins.
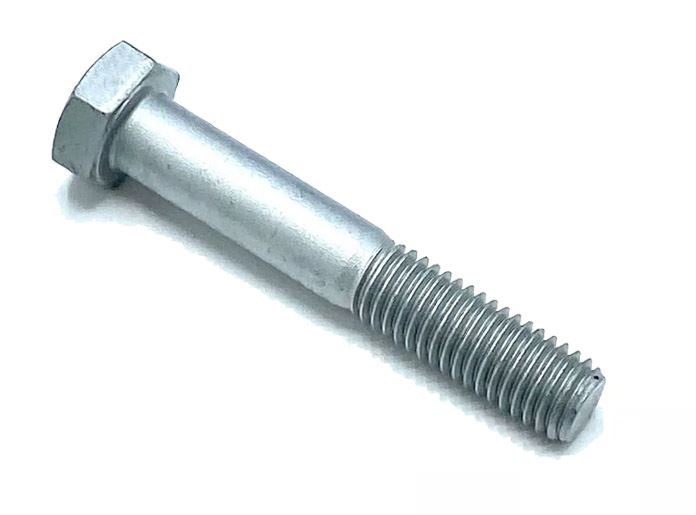
ECOMET TOP CLEAR
Water reducible hydrophobic topcoat sealer for base coats like ECOMET 500, Zinc plating and other zinc-based surfaces. The coating is applied by dip sin or spray followed by curing into oven for 150 deg c 25-30 mins.
NO HYDROGEN EMBRITTLEMENT RISK
ECOMET SOLVENT BASE COATING SERIES
EFFCO Fastener Coating Products as per ISO-10683/ASTMF-1136
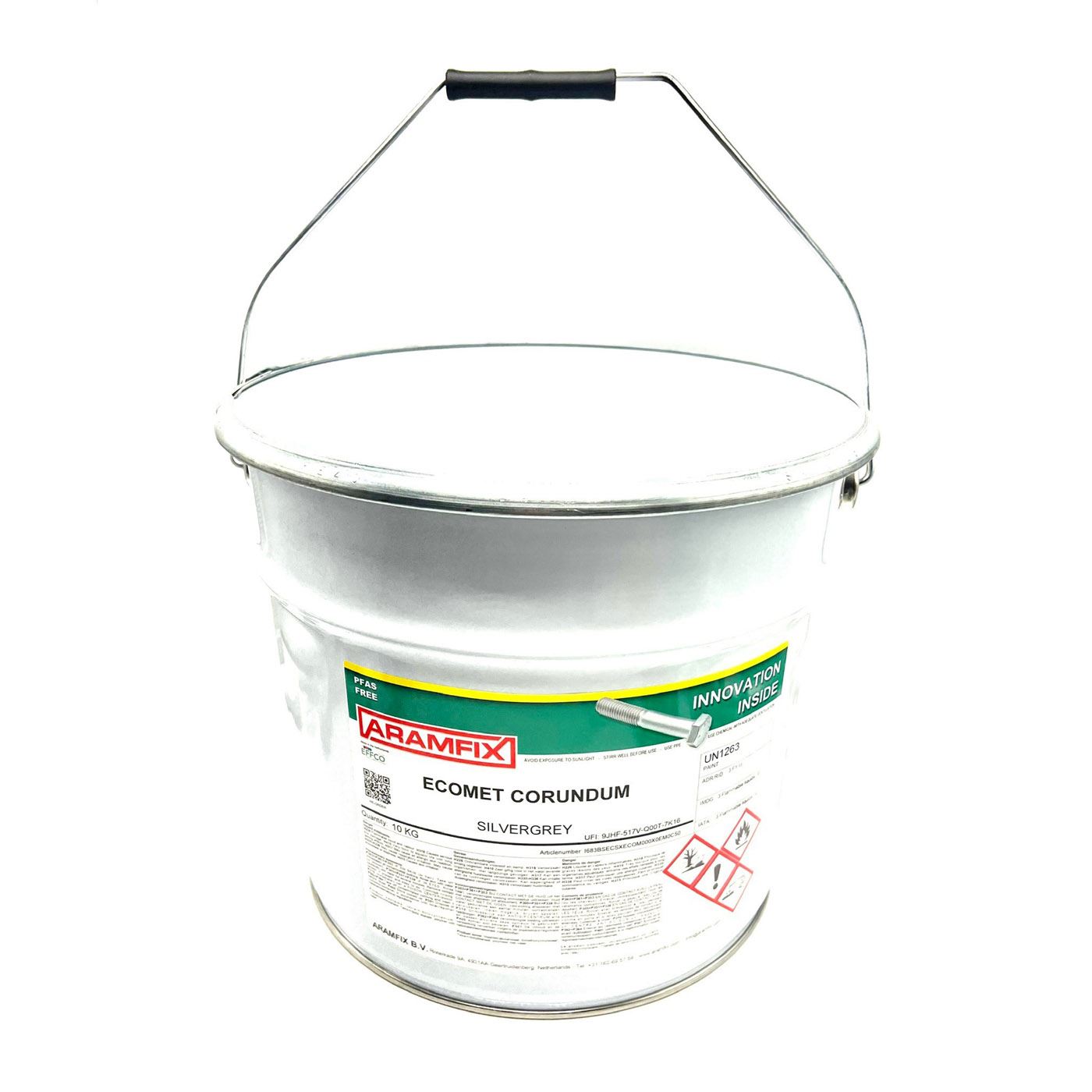
ECOMET CORUNDUM
Zinc and Aluminium Flakes combined with Corundum and other nano crystal carbon material to form never fail thin film. The coating is single pack, ECOMET solvent is require adjusting viscosity. The coating is applied by dip spin or spray method followed by curing in over at 220 deg c 25 mins.
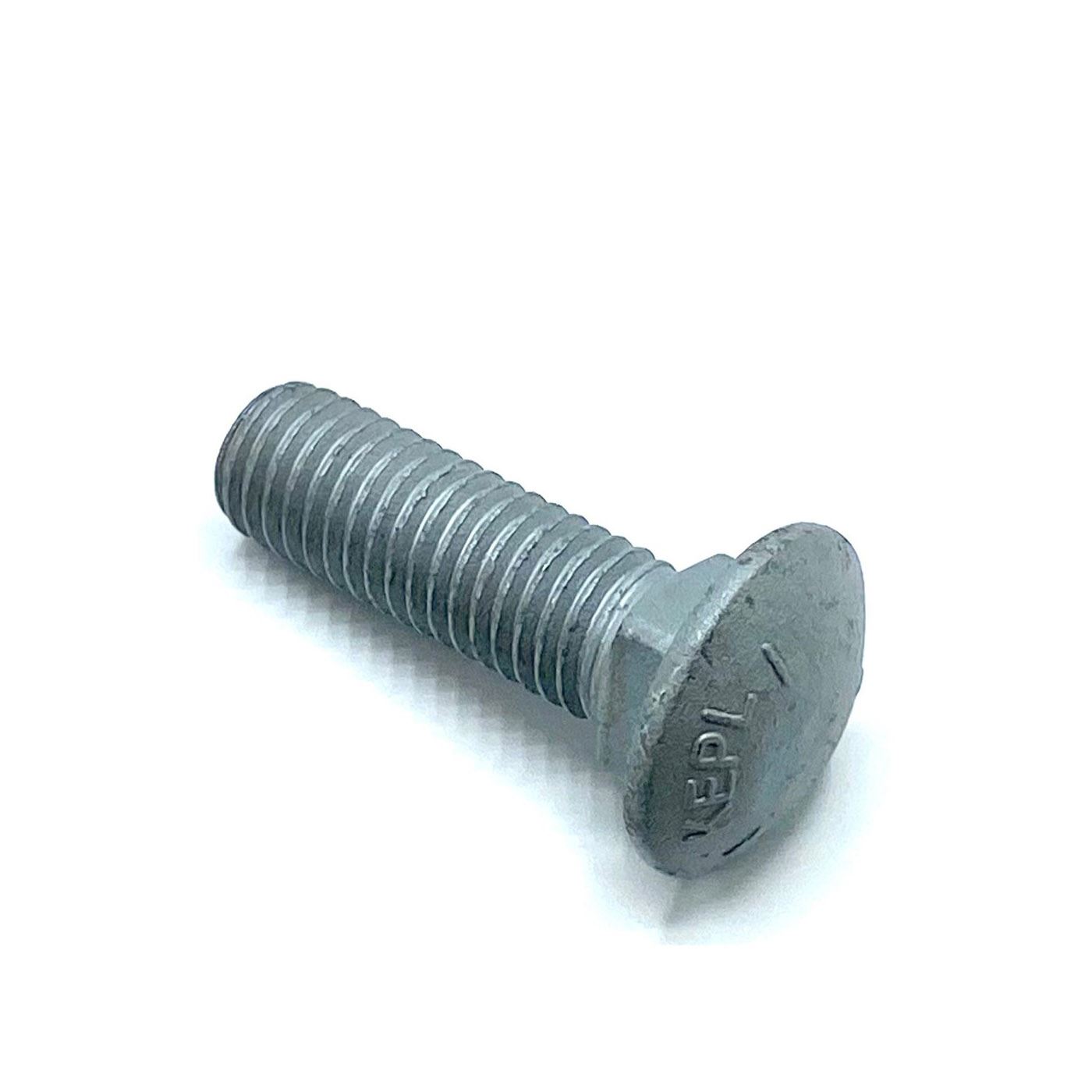
ECOMET Titanium CDG
COLD DIP GALVANISING the alternative to Hot Dip galvanising (HDG) this product has Zinc and nano crystal carbon based raw material to form 60-80 microns thickness for threaded hardware. The coating is applied by dip spin or spray method followed by curing at 220 deg c 25 mins. This is ideal alternative for HDG and mechanical galvanizing.
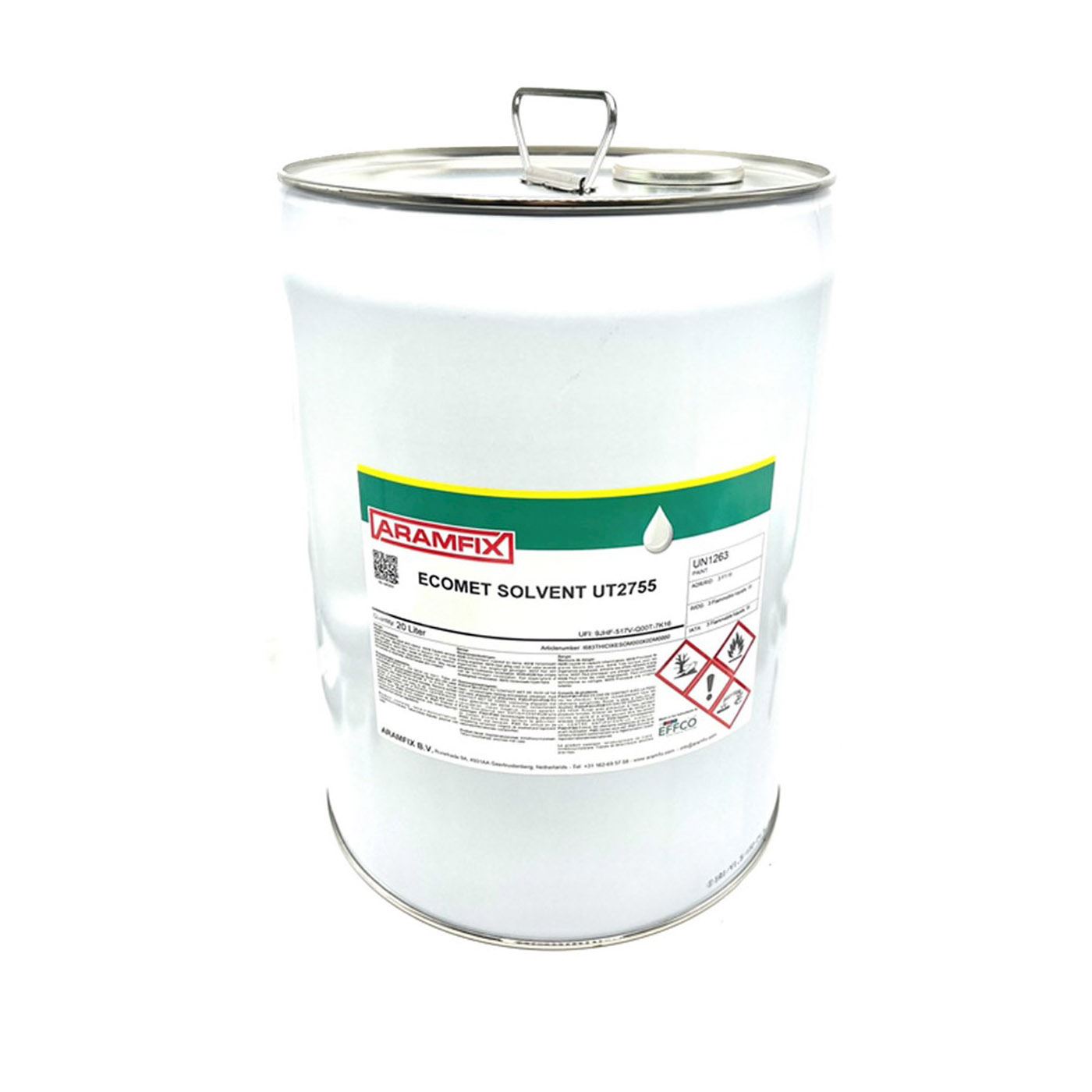
ECOMET SOLVENT
This is a solvent to be used for adjusting the viscosity of ECOMET CORUNDUM and ECOMET CDG products.
FLAWLESS APPEARANCE
DIP-SPIN MACHINE
DST 250
250mm basket
LxWxH- 1500x1500x1890mm